Customers supplying thermal transfer ribbons face significant frustration when they encounter a “Ribbon In” warning although the ribbon has been installed correctly. This prevalent problem interrupts workflow operations while generating quality concerns about supplied materials even when the actual fault exists in different places. Zebra Printer Warning Ribbon In: How Distributors Can Resolve and Prevent This Common Error
Sourcing professionals must learn how to explain and prevent the “Ribbon In” warning to reduce technical support burdens and maintain client trust. The comprehensive guide explains error origins and provides practical remedies and preventive methods while showing you how to enhance post-purchase customer support. Our content specifically serves those who handle ribbon inventory for thermal transfer printers.
What Does the “Ribbon In” Warning Mean?
The “Ribbon In” error typically surfaces when the printer falsely detects a ribbon as being installed.
- Isn’t installed
- Isn’t being detected properly
- Is installed incorrectly
- The printer detects the ribbon incorrectly because of problems with the sensor or firmware.
Thermal transfer printers that utilize coated-side-out ribbons with a 0.5” core typically encounter this error and they are standard in mid-range desktop printers across logistics, healthcare sectors as well as retail and light industrial operations.
Root Causes of the Ribbon In Warning
1. Incorrect Ribbon Loading
A common error among users is placing the ribbon in the printer with the coated side facing inward when the printer needs the coated side out (CSO) configuration. This causes sensor misreading and misalignment.
2. Dirty or Misaligned Sensors
The ribbon sensor may give false readings when dust and ribbon residue accumulates on it without any actual ribbon present.
3. Worn or Low-Quality Ribbons
Ribbon rotation becomes problematic if storage conditions are unsuitable or production results in uneven tension. The sensor gets confused by this which results in a warning message.
4. Mechanical Loading Errors
The printer could fail to register motion or detect resistance when the ribbon lacks proper tension across the spindles and the take-up roll remains loose.
5. Incorrect Printer Settings
Persistent error messages including “Ribbon In” may occur when users switch printer modes from direct thermal to thermal transfer without proper calibration.
This document provides a systematic troubleshooting guide for distributors and end users.
Step 1: Confirm Ribbon Orientation
- Take off the ribbon then use your fingernail or a card to scratch both sides to discover which side has ink.
- The coated side of the ribbon should face outside during installation.
Step 2: Reinstall the Ribbon Correctly
- Attach the supply roll to the ribbon spindle for correct installation.
- Stretch the ribbon straight from the printhead to the take-up spindle.
- Create tension in the ribbon by winding it onto the spindle before closing the lid.
Step 3: Clean the Ribbon Sensor
- Open the printer cover after turning it off.
- Carefully clean the ribbon sensor with either a lint-free cloth or sensor cleaning pen.
- Do not apply alcohol to the sensor unless the manufacturer directs you to do so.
Step 4: Calibrate the Sensor
- Access the printer menu then choose Media and Ribbon Calibration.
- Run a few labels through the printer to allow automatic detection of the ribbon and label parameters.
- Certain printer models demand the user to press and hold a button when starting up to access the calibration mode.
Step 5: Check Ribbon Tension and Alignment
- Position the ribbon in the center of its tracks and keep it smooth to avoid wrinkles.
- Verify spindle engagement and smooth operation of the take-up roll.
- Poor ribbon quality and incorrect tension will cause sensor fault-like symptoms.
Step 6: Confirm Printer Mode
- Examine the printer software or onboard screen to confirm the selection is for Thermal Transfer Mode instead of Direct Thermal.
- Printer misconfiguration makes it expect a ribbon during no-ribbon printing operations.
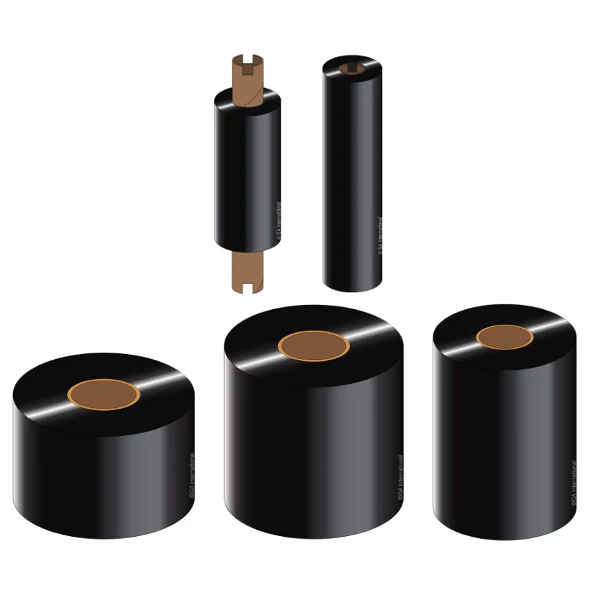
Best Practices for Preventing Future Ribbon Warnings
Distributors can help their clients avoid technical difficulties by providing thorough guidance along with premium materials.
1. Supply Only CSO-Compatible Ribbons
- All ribbon rolls need clear Coated Side Out (CSO) labels.
- Use packaging labels to display arrows or stickers that indicate the winding direction of the ribbon.
2. Add Ribbon Loading Guides in Every Box
- Include illustrated instructions for correct ribbon installation
- Provide access to online video tutorials by attaching QR codes
3. Bundle Cleaning and Maintenance Tools
- Offer printhead cleaning pens and sensor-safe wipes
- Include printed maintenance schedules with the packaged product
4. Educate Your Sales Channels
- Ensure distributors and resellers understand correct ribbon application techniques.
- Organize webinars and produce PDF guides to help users prevent ribbon sensor problems
Storage and Quality Tips for Ribbon Reliability
Temperature and Humidity
- Ribbon storage should occur at temperatures between 15–25°C and relative humidity levels of 40–60%.
- Avoid direct sunlight and high humidity
Shelf Life
- Wax: Up to 18 months
- Wax-resin: Up to 24 months
- Resin: Up to 36 months
Packaging
- Each roll should be boxed individually or shrink-wrapped with visible labels.
- Use moisture-resistant cartons for bulk shipments
Distributors who educate customers about proper ribbon use gain benefits such as improved customer relationships and increased product reliability.
Supporting customers through education creates multiple benefits.
- Reduce return rates and support tickets
- Increase customer loyalty and reorder frequency
- Establish yourself as a dependable and knowledgeable ribbon provider to distributors.
- Add value beyond just ribbon supply
When you eliminate “Ribbon In” warnings your clients will gain confidence in your product while reducing their need for third-party technical support.
Conclusion
Thermal transfer printing commonly encounters “Ribbon In” warnings yet this issue can be easily avoided. Through appropriate training and comprehensive support materials distributors can prevent customer dissatisfaction and build lasting relationships.
When you offer CSO ribbon compatibility alongside instructional support and proper packaging storage your business transcends the supplier role to become a solutions partner.
📧 sales@foyottr.com
📞 Tel: +86-592-6018318
🌐 Visit Our Website
💬 Contact Us for Bulk Ribbon Support
FAQ
What causes the “Ribbon In” warning?
The “Ribbon In” warning occurs because of improper ribbon loading alongside a dirty sensor or incorrect printer settings.
To determine if your ribbon is coated side out (CSO) you need to scratch both sides of the ribbon with a coin or paper edge and observe that the side which shows a visible mark is the coated side.
Use a coin or paper edge to scratch both sides of the ribbon to determine which side shows visible marks. The ribbon side which shows visible scratches from testing with a coin is the coated (inked) side.
Can I reset the ribbon sensor manually?
The ribbon sensor can be reset by conducting a calibration procedure in either the printer’s control panel or via driver software.
Cleaning the ribbon sensor is safe as long as you use a lint-free cloth or a sensor-specific cleaning tool without alcohol.
Cleaning the ribbon sensor requires a dry, lint-free cloth or a tool made specifically for sensor cleaning. Avoid alcohol unless specified.
Bad quality ribbon can trigger “Ribbon In” errors.
Absolutely. Any ribbon that is wrinkled or unevenly wound or has expired will confuse the sensor and trigger this warning.
📧 sales@foyottr.com
📞 Tel: +86-592-6018318
🌐 Visit Our Website
💬 Contact Us for Bulk Ribbon Support